Advanced Physics Dynamics
Introduction
The current implementation of the Physics Engine in Experior 7 presents difficulties in accurately simulating the dynamics of loads under certain scenarios commonly found in conveying system applications. This may partially or entirely alter the results of simulation and emulation models, requiring workarounds to overcome these issues.
To address these challenges, a new implementation called Advanced Dynamics has been developed to provide a generic solution that covers a broad spectrum of complex dynamics scenarios presented in case conveying and pallet conveying systems, with respect to the motion of loads produced by forces exerted by conveyors. However, it is not within the scope of this new implementation to provide a solution that represents a 1:1 version of real physics (e.g., material deformation), considering the computational limitations of real-time simulations.
Development
The following section describes the main points that have been reworked to significantly impact the overall physics engine.
Load transition
Problem
- The displacement of the load is affected, either partially or totally, by the collision between the load and the belt that occurs during the transition in merge and divert sections.
- Flawless transitions depend on the geometry and dimensions of the load.
- Load orientation (Yaw) is affected during the transition, regardless of whether the configuration is straight-straight or straight-curve sections.
Solution
Whenever there is a collision between dynamic actors (i.e. loads) and static actors (i.e. belts), PhysX generates contact points that the contact solver uses to determine the velocity and position of the load. However, before the contact solver is applied, the properties of these contact points, such as the vector orientation, are modified to ensure a smooth transition, regardless of the geometry or dimensions of the load. The primary purpose of contact modification is to enable seamless transitions between conveyors, without requiring the use of ramps.
Contact Points
Problem
Loads can exhibit unrealistic behaviors in certain scenarios where they come into contact with more than one surface simultaneously. This is because only the greatest velocity is applied. The current implementation lacks the capability to retrieve information about the contact points generated by the surfaces and the load.
Contact Points
Solution
PhysX filter allows retrieval of information related to contact points generated by collisions between dynamic and static actors. This makes possible to develop proper mathematics which considers the distance between the load’s center of mass and the position of each contact point to apply forces and torques correctly.
Friction
Specifically, this refers to the friction force a conveyor surface applies to a load. Experior 7 calculates this friction force when the speed of the surface motor on a belt is different from zero. When the speed of the surface is zero, the PhysX engine from Nvidia will take over these calculations.
Note: Patch and Two directional refer to the two friction modes from Nvidia PhysX supported in Experior 7. This only affects the friction force when it is being handled by the PhysX engine (i.e.: surface speed is zero). The key differences are:
- Two-directional combines the load and the surface friction coefficients for the force calculations, whereas Patch gives priority to the surface friction coefficients.
- According to the Nvidia PhysX documentation, Patch mode has better performance.
- Two-directional mode is more realistic, especially with static friction, as patch mode has unrealistically strong static friction. This behaviour is most noticeable when a load is touching surfaces with non-zero velocity and zero velocity simultaneously.
In Experior 7, the friction mode can be set through the command line arguments (patch is the default value). Experior 6 only supports the Two-directional mode.
Problem
The friction force calculations made by Experior 7 and the PhysX engine are inconsistent. An acceleration-deacceleration test showed this, where a load starts from rest on a conveyor. Afterward, the motor is turned on with a speed of 1.5 m/s and then is turned off (motor acceleration and deceleration are disabled). The following images show the load speed plotted against time. As the same physical phenomenon (dynamic and static friction) is responsible for the acceleration and deceleration of the load, we would expect the plotted curves to have a symmetrical behaviour. However, It is noticeable that the load behaves differently when accelerating and decelerating. This shows the inconsistencies between the force calculated by Experior 7 and the PhysX engine.
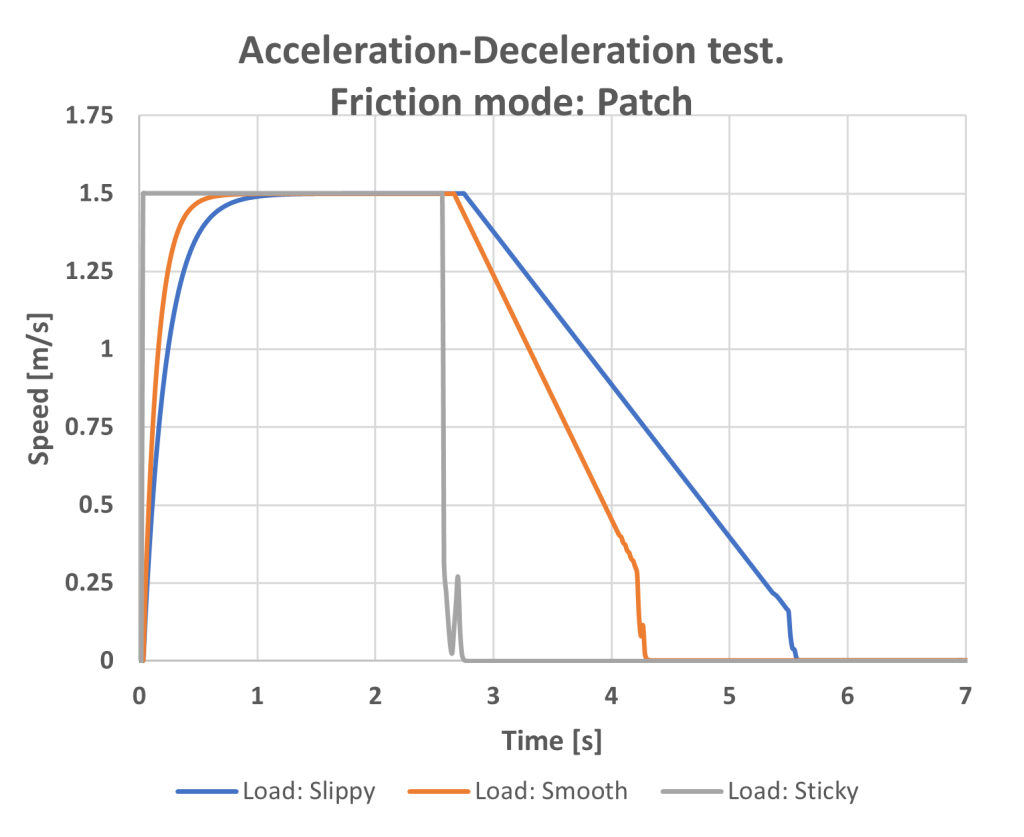
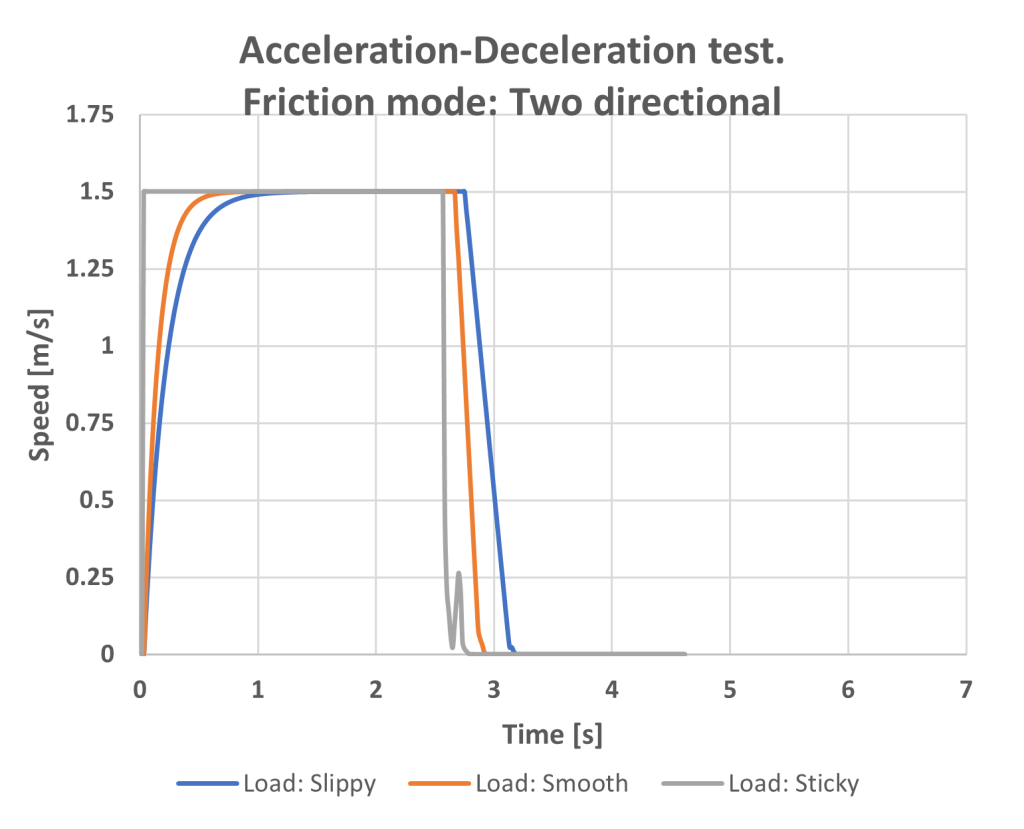
Solution
According to the Nvidia PhysX documentation, the friction force is calculated using the Coulomb friction model. To make the calculations from Experior 7 more consistent, we are now calculating friction force based on the Coulomb friction model. The following images show the results of the acceleration-deceleration test with the new friction calculations. Due to the symmetry in the curves, we can see that the friction force of the conveyors is now consistent when the motors are on and off.
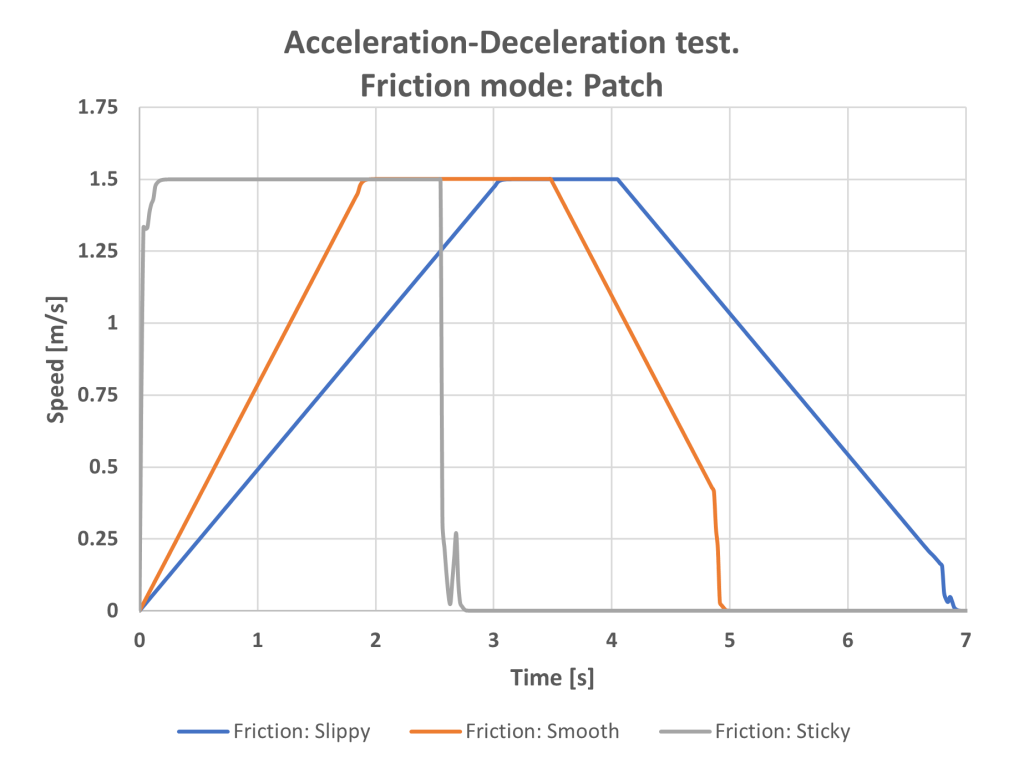
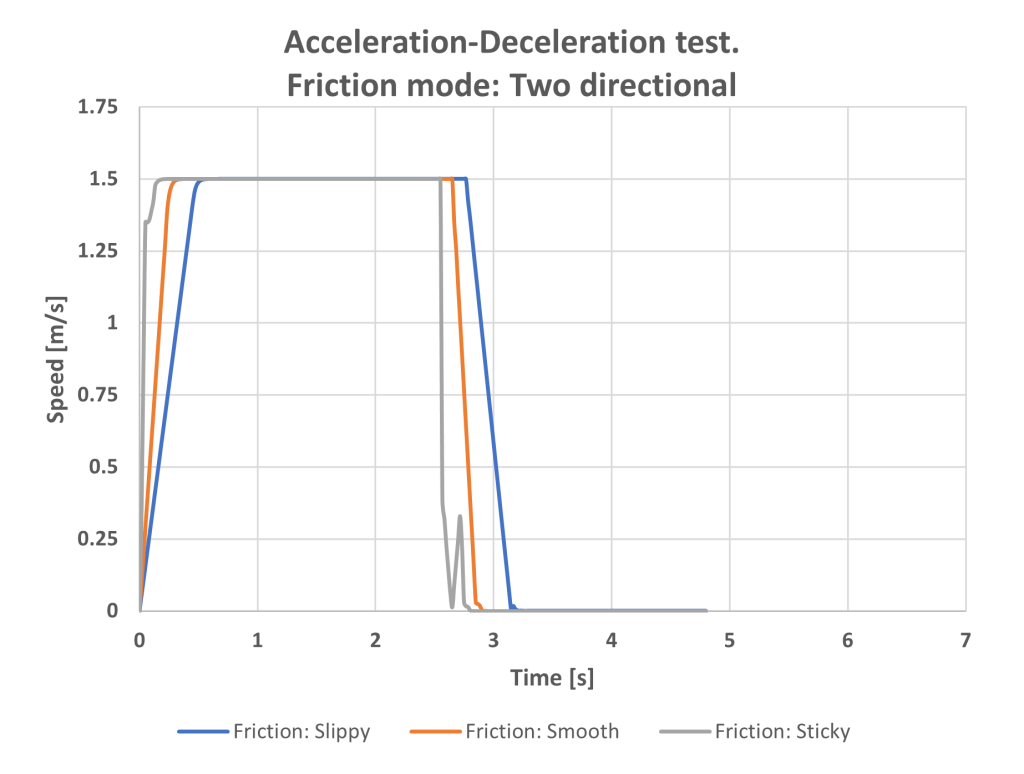
Load Trajectory
Problem
When the surface in contact uses sticky friction, Experior directly defines the load’s LinearVelocity property. However, this approach is inconsistent with PhysX, which computes all the forces exerted on a dynamic actor to determine its velocity and position. Furthermore, when the friction is not sticky, forces and torques are applied without regard of the surface’s orientation.
Load Trajectory
Solution
- Forces and torques are calculated based on the alignment of the surface and the information extracted from the contact points.
- During transitions from straight to curve and from curve to straight, forces and torques are applied independently to each surface. This is determined by the position of the center of the load.
- Remove the ramps from the conveyors.
Results
The following images show a comparison between the current implementation and Advanced Dynamics regarding the orientation of the load and its trajectory during the loop configuration (straight-curve-straight-curve).
Stacks
Problem
The current physics engine configuration does not allow for stable stacking or displacement due to the default collision detection system (Permanent Contact Manifold). PCM is a distance-based collision detection system that can generate fewer contacts, potentially reducing the stability of tall stacks when simulating with insufficient solver iterations.
Solver iterations refer to the minimum number of position and velocity iterations used by the contact solver behind the scenes to determine the velocity and position of a load.
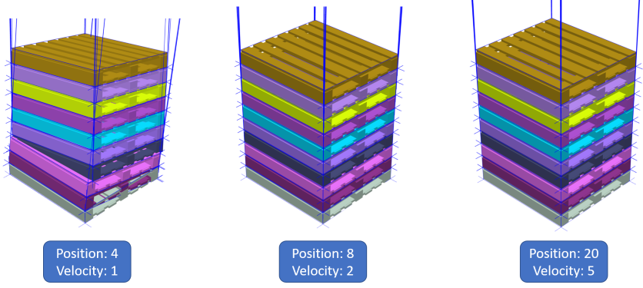
Solution
The physics engine configuration now includes a new feature called “Average Point”. This feature generates additional contacts per manifold to represent the average point in a manifold. It can stabilize a stacking effect when only a small number of solver iterations are used. The following videos demonstrate the difference when increasing the number of solver iterations from P:4,V:1 to P:20,V:5.
Thanks to the new implementation, stacking and destacking processes no longer require additional functionalities or logic to achieve the correct behavior of the stack (e.g., the use of Group() and Ungroup() from the Load class). However, limitations from PhysX are still present when using a stack with a significant number of loads. The next two videos demonstrate the stacking and destacking processes, where the sensor between the forks only attaches to the load making contact.
Sleep Threshold
Problem
The PhysX solver continues to execute even when the load is not moving, resulting in unnecessary consumption of computational resources. In the video, it is evident that the arrow of each load which represents the linear velocity, keeps moving around continuously, even though the loads are completely static.
Solution
Each dynamic actor contains a property called SleepThreshold, which sets the mass-normalized kinetic energy threshold below which an actor may go to sleep. Once an actor goes to sleep, PhysX will not report or notify it.
If a load on top of a conveyor is in a sleeping state, it will automatically awaken once the motor starts (CurrentSpeed != 0f). This is due to the notification from the motor to the PhysX engine through the method BeginStart(). However, it will take one more frame for the physics engine to move the load.
It’s important to note that any motor developed using inheritance from the Electric class must use the method BeginStart when starting the motor.
Risks / Side Effects
To address the issues that were disclosed, it was necessary to implement new functionalities, which may have some unintended consequences. The following section outlines the potential risks associated with each of the proposed solutions.
Performance
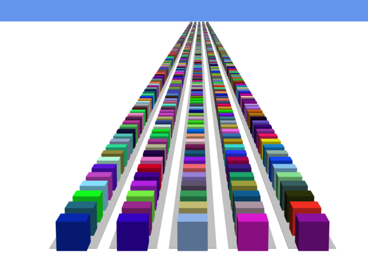
Performance decreased 18%
Processor: i7-9750H CPU 2.60 GHz
Ram: 16 GB
Nvidia GeForce RTX 2070
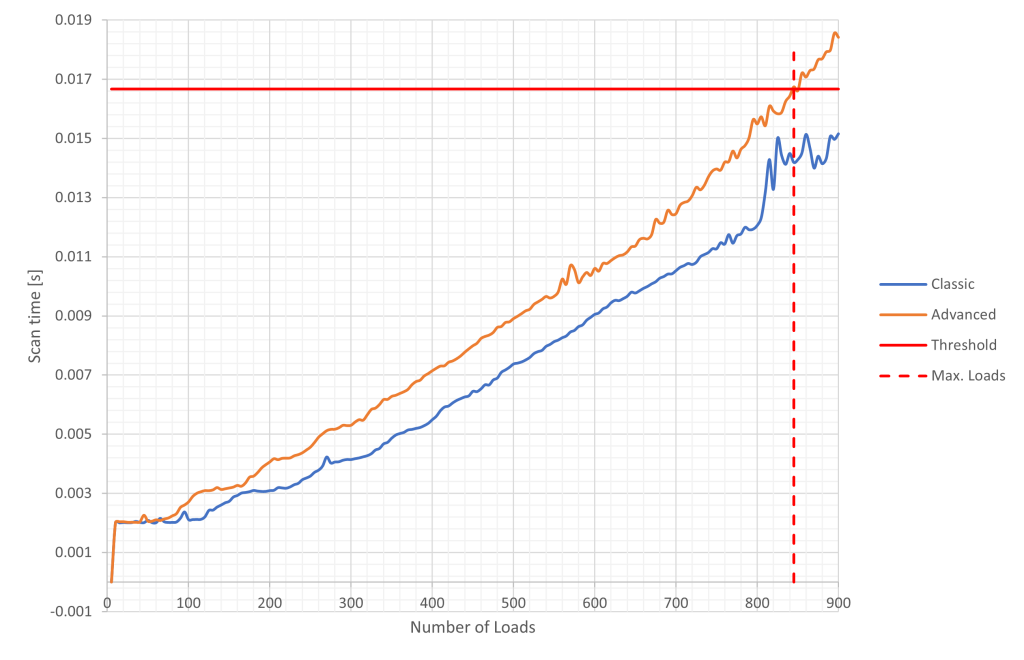
A test was conducted to compare the performance of Advanced Dynamics with the current implementation, Classic Dynamics, which was considered a benchmark due to its efficiency. As shown in the image, Classic Dynamics is capable of handling 850 loads without exceeding the 16 millisecond threshold (the threshold is determined by the cycle task frequency of 60Hz), whereas Advanced Dynamics surpasses it. Based on the results of this specific test, Experior’s performance decreases by approximately 18%.
It is important to note that performance can vary due to hardware specifications, as well as the size of the model and assemblies contained within it.
Precision to represent reality
In some specific cases, uncertainties about the real-life dynamics of the load may arise due to the broad spectrum of complex scenarios and the lack of physical facilities to test them. Therefore, we are open to discussing and improving based on your feedback.
Although the mathematics defining the dynamics of the load and configuration of the PhysX engine have been reworked, computational limitations still persist due to the contact solver capacity. This is particularly evident when implementing tall stacks (more than 15 loads) or handling loads with very small dimensions. This limitations are expected to improve after updating the PhysX engine version in the near future.
False Expectations
Users should not expect to obtain the same results when using Advanced Dynamics as when using Classic Dynamics with regards to load dynamics, particularly when modifying the friction coefficients. The old implementation was developed in a specific way to overcome problems resulting from the lack of information and default configuration of PhysX, such as very high and low coefficient values. As shown in the following video, using the smooth friction type from Classic Dynamics will not produce the same results in Advanced Dynamics.
Implementation
- To fully take advantage of the advanced dynamics, it is strongly suggested to remove the ramps of the belts used in your catalog. A new query property Experior.Core.Environment.Engine.AdvanceDynamics has been introduced, so that developers can handle the proper removal of ramps based on the physics engine dynamics.
- Users have the option to select the Physics engine dynamics type through the CLA (Command Line Argument) -physicsenginedynamics “advanced”. By default, Experior 7 will use “classic”. This parameter can be set from the cmd or the shortcut configuration as the following images show.

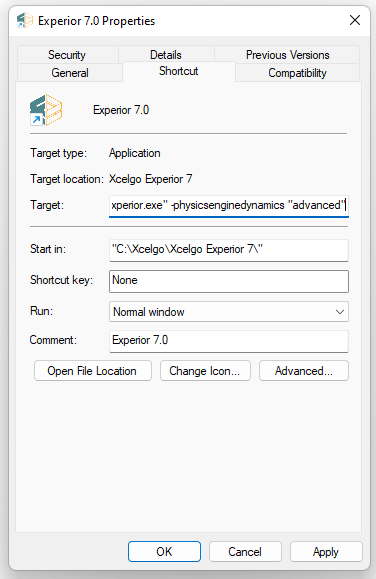
- MinPositionIterations and MinVelocityIterations properties have been added to the class Load.
- Global SleepThreshold property set automatically to 5e-5 if advanced dynamics is used. Nevertheless, the property SleepThreshold is available from the class Load.
- Visualization of contact points are displayed in debug visualization mode when using advanced dynamics.
- New friction coefficient values have been defined. Experior will automatically set the appropriate friction coefficient based on the selected physics engine dynamics. The following image displays the friction coefficient values defined for advanced dynamics mode.
